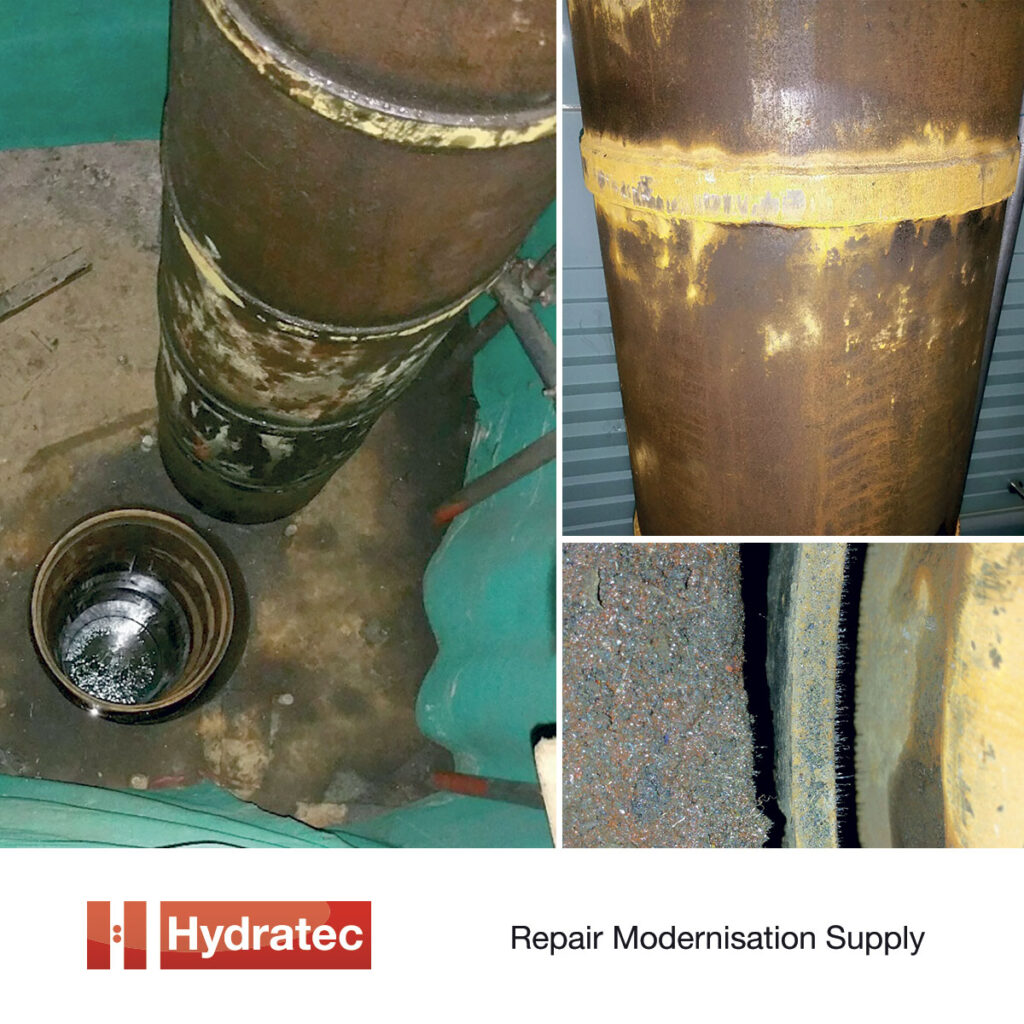
There are many hydraulic lifts where the ram connects under the car frame and the cylinder sits in the ground; this arrangement is generally known as a borehole system.
A borehole, typically between 500 and 750mm diameter, is drilled into the ground. A steel liner is then lowered into the borehole, which is capped at the bottom with either with a steel plate or with a concrete plug. The liner is plumbed and then backfilled between the borehole and the outside of the liner with concrete. Steelwork is then added above the liner, to provide a fixing point for the suspension plate which is attached to the cylinder. The cylinder is then lowered into the borehole, with appropriate protection being applied as it lowered down.
Over the years, the steel liner or concrete plug can deteriorate and allow water into the liner. Well applied cylinder protection will protect the cylinder from corrosion, but it has to be applied correctly. Where the integrity of the liner is breached, water will enter the liner. In a lot of cases, this is mistaken for oil, the reason being that oil floats on water. Looking down into a borehole, you will see any residual oil on the surface, and it is often assumed that the borehole must be full of oil. In 99.9% of cases it is a few litres of oil floating on top of a large quantity of water. You will often find the level of the fluid in the borehole rising and falling; this is caused by the rising and falling of the water table, rather than any inherent problem with the cylinder.
It is always advisable to confirm the source of any unidentified fluid, and it is vitally important to monitor any unexpected oil loss from the tank. Where a cylinder is suspected of leaking oil out of the casing, a simple test is to isolate the control valve and monitor the lift movement, always taking into account any loss from the ram seals and unexposed hose runs. If there is further cause for concern, or as a precaution, a CCTV inspection of the borehole and cylinder can be carried out prior to a two-times pressure test being implemented. The CCTV inspection is used to determine the integrity of the cylinder protection before pressure testing.
Our team of engineers have carried out many successful inspections and pressure tests, including our recent test of a Bucher BZG320 cylinder to 80bar, which simulated a load of just shy of 65,000kg.
We are also able to reline your existing borehole to prevent further water ingress subject to clearances. This involves the removal of the cylinder (usually replaced at the same time) with a new polyurethane liner sunk into the existing borehole. The annulus between the old and new liner is then filled with ‘Bentonite Clay’ pellets which react with the water to hold the new liner in place.
If you’d like to find out more about the process, and need some specialist advice, please contact us.