Hydraulic Scenic Lifts, Direct Acting Borehole – Water Ingression
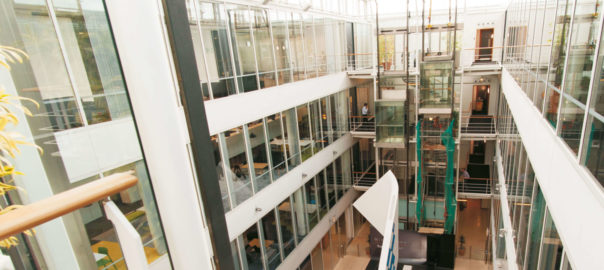

top image Steel sleeve pressed into place, liner being readied for lowering into sleeve · bottom image Steel liner welded and ready for lowering into the sleeve
BACKGROUND
Originally installed in the early 1990s, the four scenic lifts were all experiencing problems with water ingress into the boreholes, resulting in lift break-downs due to overheating (despite 12kW oil coolers being fitted).
The building owners had become concerned about the level of water ingress into two of the four boreholes and the high energy consumption. The lifts are situated in pairs at each end of the atrium and the water ingress problem affected all four lifts, however, the problem was most acute on the two lifts which diagonally opposed each other.
OUR BRIEF
Hydratec was tasked with replacing the liner. Over the years, Hydratec has re-lined several boreholes using MDPE piping where there has been a problem with water ingress.
The process is straightforward, the water in the borehole is pumped out, the new liner is installed in sections which screw together with silicone to seal the joints. The liner is then weighted with water and once fully assembled, it is plumbed.
Bentonite pellets are filled around the annulus (between the old and new liners) and left to swell overnight to seal the liner in position. Once the bentonite has sealed, the water holding the liner in position can be pumped out of the liner and the new cylinder can be installed.
To view the full case study, and Hydratec’s solution, download a PDF of the case study here.